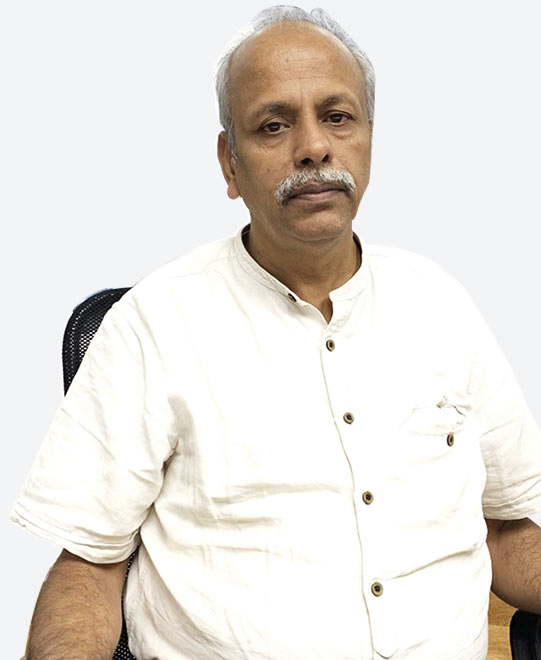
From the CEO’s Desk
N.Rajagopalan
Chief Executive Officer
We offer wide range of offering in Denim category, plan to introduce jeans for modern youth in mass segment by leveraging our channel both MBO and EBO. Our intent is to make more trendy range of categories in jeans, knits and woven incoming days to woo young consumers who fancy global labels and brands. Challenges for us to make trigger more attractive both in terms of style and right price offering to ensure faster conversion in our EBO and MBO channels.
“Trigger will give value to consumer by offering continuously new styles and fit with sustainability. Our vision is every 3rd Indian consumer should own at least one pair of Trigger jeans.”
Our Policy
Sustainability Policy
KGDL operates in full compliance with the applicable laws, rules and regulations. Being one of the world’s largest producers of denim, “we realise that our environmental responsibility too is among the largest.
We have taken more initiatives to improve the environmental performance and reduce the carbon footprint. We believe that our environmental performance is the direct result of our team of talented professionals and state of the art infrastructure with commitment to continuous improvement.”
About
Company Background
KG Denim Limited was started by K Govind Swamy Naidu in 1932, and Trigger Apparels Limited by KG Baalakrishnan in 1996. The group has an annual turnover of $350 million. It is one of the leading denim apparel manufacturers in India and has separate units for yarn and apparel manufacturing.
Trigger Apparels, a 100 per cent subsidiary of KG Denim, is engaged in the domestic marketing of Trigger branded jeans, trousers, shirts, t-shirts and other allied products. Sales are made through EBOs, company operated retail outlets and factory outlets, besides C&F agents on a consignment basis. The garments are produced through vendor operations. The products are ready-to-wear jeans and cotton trousers of varying colours, shades, weaves, designs, styles, fabrics and washes.
INTIATIVES
Sustainability Initiatives
Green initiatives: There have been many such initiatives. Highlights:
- ‘Green to Blue is denim process; Blue to Green is our progress’ is the governing theme of process activities of KGDL;
- Access to clean water is considered as the heart of N Rajagopalan Chief Executive Officer all processes and projects in addition to its conservation;
- Ensuring environmental sustainability through zero discharge, resource conservation, wastage reduction and prevention of pollution;
- Recovery and reuse of byproducts generated in the process.
Energy saving initiatives: KGDL is contributing to the nation in reducing the power demand by operating its own power plant by using biomass as fuel. The steam exhaust from the turbine after generating power is used for processing. Recovery of condensate water from processing, the caustic recovery plant and evaporator, and reuse of the same in the processing results in additional water and steam savings. Some details:
- The unique counterflow system in the fabric processing gives water and steam saving;
- Extensive usage of LED lights and transparent sheets wherever possible reduces the lighting power load;
- Collection and re-use of blowdown water in the power plant boiler saves water and heat energy;
- Heat recovery system is installed in the bleaching, mercerizing, pad steamer and caustic recovery plant for effective usage of heat energy by reducing the steam consumption;
- Heat is recovered from the hot flue processing machines and reused.
- All freon gas air conditioners in the production site are replaced by introducing gas free VAM (vapour absorption machine) technology.
- Air cool condenser is used in the power plant to avoid evaporation loss in the water-cooling process.
Advanced technologies and minimisation of chemicals: KGDL’s innovative concepts reduce the core chemicals usage in the processing by implementing advanced technologies like prereduced liquid indigo, salt-free reactive dyeing, and cotton / polyester dyeing in one step. The trials of salt-free denim dyeing are under way. KGDL is committed to saving the environment by reducing the quantity of chemicals used in processing. The advanced technology of liquid indigo system is reducing 60–70 per cent of sodium hydrosulphite and caustic soda consumption in denim processing.
The entire dyeing process is controlled through DCS. All machine parameters, flow control, dosing systems and consumption of utilities are continuously monitored through on-line trend. The variations in the processing are immediately alerted for taking corrective action.
KGDL has introduced another innovative process for reactive dyeing of all cellulosic fabrics. This process is a continuous one without any salt, silicates or urea. Rapid dye fixation is carried out by maintaining the humidity and temperature in a constant ratio. To meet leading brand requirements globally with high fastness properties, KGDL produces all colour ranges from pale to jet black through this salt-free technology. This process consumes less energy, water and alkalis. High quality dyestuffs with more fixations result in very less amount of pollutants in the washwater.
Another advanced dyeing technology is to dye cotton / polyester blended fabrics in one step without intermediate reduction clearing process which results in less water, chemical and energy usage.
Effluent treatment plant: The effluent treatment plant is a zero discharge plant adopting the latest process techniques in effluent treatment and more than 90 per cent wastewater is reclaimed through a state-ofthe- art disc membrane reverse osmosis process. Reclaimed water is reused in processing, enabling greater control over bleaching and dyeing against water from natural sources that have varied parameters depending on the season. The quality of treated water is much above the state legal norms. However, its quality is being ensured through in-house lab, third-party lab and state pollution control board lab at defined intervals. In addition to this, testing of parameters as per ZDHC wastewater guidelines is also carried out twice a year.
Greenhouse gas monitoring system: KGDL has started to measure its greenhouse gas (GHG) emissions as per ISO 14064-1, which is an international standard for GHG emission inventories and verification. KGDL has achieved ISO 14064 certification using part I guidance along with the WBCSD Green House Protocol. This covers identification of organizational and operational boundaries, identification of emission sources, collection of activity data and emission factors, emission calculation method and its removals to reduce GHG emissions. For reducing the adverse environmental impact of operations, “we focus on some areas including energy, water conservation, GHG emissions, reducing the generation of waste and protection of biodiversity across the locations.” Reduction of carbon emission is planned through reducing fossil fuel consumption and increasing the biomass. The generation of in-house biomass is achieved in extracting rice bran oil through solvent extraction plant. The residue is a perfect biomass fuel (de-oiled rice bran) that is used in power generation. The GHG emission measuring and monitoring system has been followed since 2013 and the trend is described below:
- Air emission: KGDL is complying with all applicable laws and regulations pertaining to emission to the air. The stack emission monitoring is carried out through online Japanese technology and measured at frequent intervals with the help of outside agencies and state pollution control board. Biomass-based co-generation (steam and power) power plant is fully monitored through DCS and its efficiency is always maintained above 80 per cent and thus CO2 emissions are reduced maximum. The emissions in the boiler are screened and controlled through back filters and ESP system.
- Waste management: KGDL has established a management system for different types of waste handling, storage and disposal. The waste storage areas are properly marked, covered, paved and protected from fire hazard and rain. The disposal of hazardous wastes like used containers, used oils, e-waste and used batteries are carried out as per the guidance of state pollution control board in a safe manner. KGDL is identifying and reusing the generated wastes like polybags, hessian sacks, paper cones, cheeses, wooden platforms and yarn waste. The food waste generated in the canteens are used to generate the biogas for cooking.
- Certifications: KGDL has been certified with ISO 9001:2015 for quality management system, ISO 14001:2015 for environmental protection and OHSAS18001:2007 for occupational health and safety. The company has been accredited with GOTS for organic products and GRS and RCS (Recycled Claim Standard) for recycled product processing. The company has a full-fledged laboratory with a highly qualified, experienced and dedicated team of technical experts, and has obtained NABL accreditation in chemical and mechanical testing complying with latest version of quality system as per ISO/IEC 17025:2005.
Our Products
Sustainable Products
Fabrics: KGDL manufactures only sustainable products through effective control of chemical procurement and adopting an effective chemical management system. The processing chemicals are tested by a third-party lab in Germany to ensure that chemicals are free from restricted substances.
KGDL uses sustainable products like organic cotton, recycled cotton, recycled polyester, etc, besides adopting sustainable processes like saltfree denim dyeing.
The products made by KGDL are eco-friendly and complying with OEK-TEX -class-I (babywear) requirements. Moreover, all finished products are frequently tested in third-party laboratories for ensuring compliance with RSL of various brands and REACH requirements.
Denim washes: KGDL does all kinds of sustainable washes and the laundry is equipped with advanced machinery to achieve them consistently. Energy saving, optimal utilisation of steam and power together are the prime motto for the operations team.